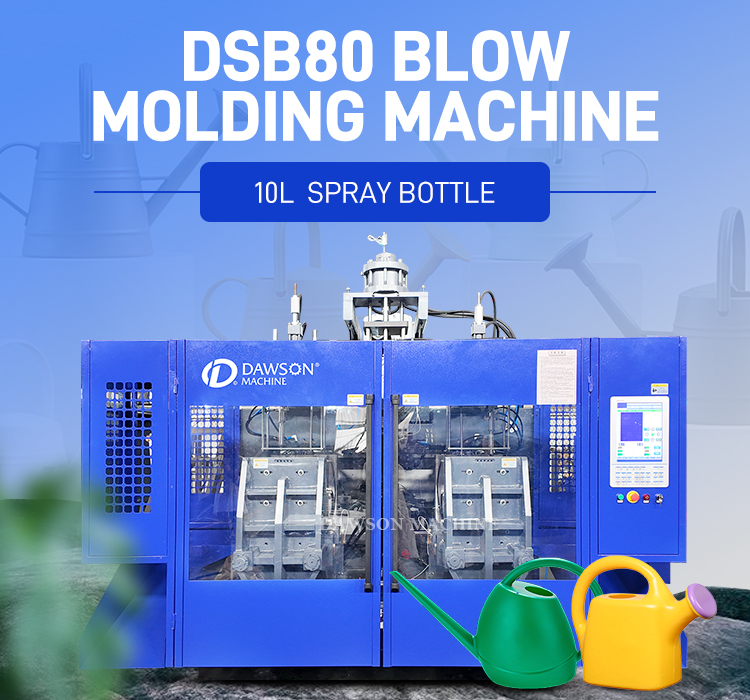
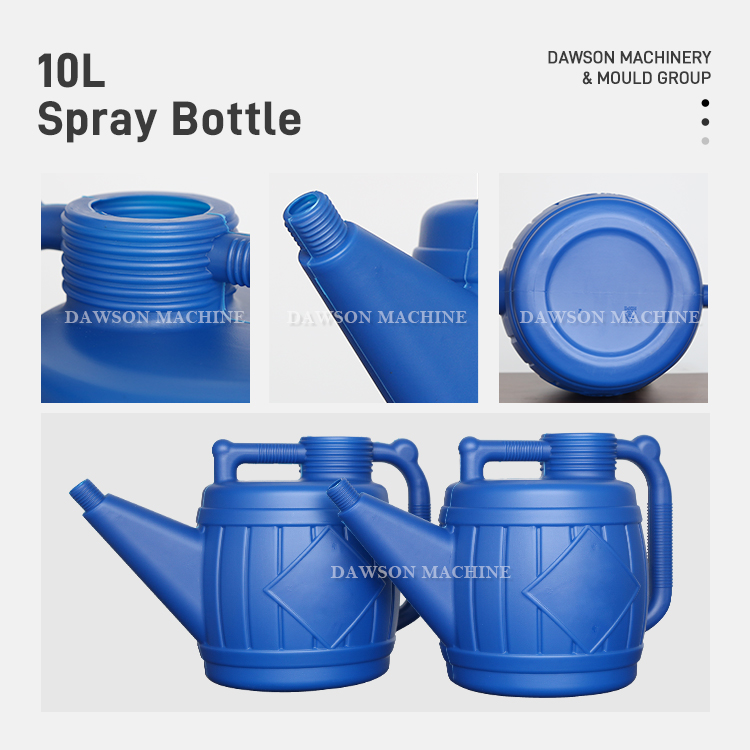
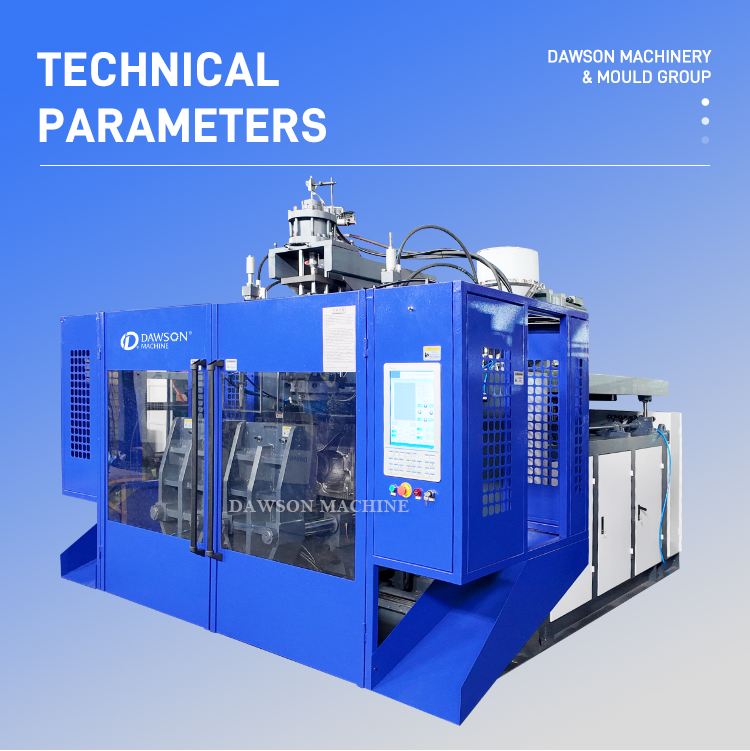
Parameters | Units | DSB70-10L | DSB80-10L |
Screw diameter | mm | 70 | 80 |
ScrewL/Dratio | - | 24 | 24 |
ScrewRPM(50HZ) | r/mm | 10-70 | 10-60 |
Extrusion capacity per hour(PE) | kg/h | 70 | 110 |
Number of heaters | - | 3 | 4 |
Opening stoke | mm | 600 | 600 |
Platen size | mm | 450*520 | 450*520 |
Clamping stoke | mm | 200-650 | 200-650 |
Clamping force | KN | 110 | 110 |
Dry cycle time | S | 9 | 14 |
Cooling water pressure | Mpa | 0.2-0.3 | 0.2-0.3 |
Cooling water consumption | L/min | 60 | 60 |
Air pressure | Mpa | 0.8 | 0.8 |
Compressed air consumption | m³/min | 0.8 | 0.8 |
Machine Dimension(LxWxH) | mm | 3800x2100X2950 | 4000x3100X3150 |
Machine net weight | T | 7 | 10.2 |
Double head central distance | mm | 200 | 200 |
Triple head central distance | mm | 150 | 50 |
Four head central distance | mm | 100 | 100 |
Power Unit |
|
|
|
Extrusion motor | KW | 22 | 30 |
Extruder heating power | KW | 14.2 | 16 |
Power of die heating zone | KW | 4
| 4 |
Hydraulic motor | KW | 11 | 11 |
Total power | KW | 55.2 | 65 |
Bridging Efficiency and Responsibility: The Evolving 10L Spray Bottle Extrusion Blow Molding Machine
The 10L Spray Bottle Extrusion Blow Molding Machine is not just a workhorse of plastic production; it is a testament to how manufacturing equipment can adapt to the changing tides of industry demands, environmental regulations, and technological progress. Beyond its core function of shaping plastic into 10L spray bottles, this machine is undergoing a transformation that merges high productivity with a strong sense of environmental responsibility, while also catering to the need for flexible and responsive manufacturing.
Harmonizing with Environmental Standards: A New Imperative
In an era where environmental consciousness is no longer an option but a mandate, the 10L Spray Bottle Extrusion Blow Molding Machine is being reengineered to align seamlessly with stringent environmental standards. One of the key areas of focus is reducing carbon footprints during production. Modern machines are equipped with energy recovery systems that capture and reuse the excess heat generated during the extrusion process. For example, the heat dissipated from the extruder barrel and die head is channeled to preheat the incoming plastic pellets, reducing the energy required to melt the raw materials. This not only cuts down on energy consumption but also lowers greenhouse gas emissions, making the production process more sustainable.
Moreover, these machines are now designed to minimize plastic waste at every stage. The parison, which is the initial tube of molten plastic, is precisely calculated to match the exact volume needed for the 10L spray bottle. Advanced software algorithms determine the optimal parison length based on the bottle's design, ensuring that there is little to no excess plastic that would otherwise be trimmed off and discarded. Additionally, the trimming process itself has been optimized. The trimmed plastic scrap, which is inevitable in some cases, can be directly fed back into the extruder for reuse, creating a closed-loop system that reduces reliance on virgin plastic and minimizes waste sent to landfills.
Smart Production Flows: Beyond Basic Automation
While automation has been a part of the 10L Spray Bottle Extrusion Blow Molding Machine's functionality for years, the new wave of smart production flows takes it to a whole new level. These machines are now integrated into interconnected manufacturing ecosystems, where they communicate with other equipment, inventory management systems, and even suppliers in real time. For instance, when the machine detects that the supply of plastic pellets is running low, it can automatically send a notification to the supplier's system, triggering a replenishment order. This not only prevents production halts due to material shortages but also optimizes inventory levels, reducing storage costs and the risk of material degradation.
Artificial intelligence (AI) is also making its way into these machines, revolutionizing quality control. High-resolution cameras installed at the ejection point of the machine capture detailed images of each 10L spray bottle as it comes out of the mold. AI algorithms then analyze these images to detect even the tiniest defects, such as micro-cracks, uneven wall thickness, or imperfect thread finishes on the bottle neck. What sets this apart from traditional quality control methods is the AI's ability to learn and improve over time. It can identify patterns in defects, such as a sudden increase in uneven walls, and trace the root cause back to specific machine parameters, such as fluctuations in extrusion speed or blow pressure. The machine then automatically adjusts these parameters to rectify the issue, ensuring consistent quality without human intervention.
Adapting to Market Volatility: Flexibility as a Core Trait
The market for 10L spray bottles is subject to constant fluctuations, driven by changing consumer preferences, seasonal demands, and emerging industry trends. The 10L Spray Bottle Extrusion Blow Molding Machine is now being designed with flexibility as a core trait to navigate these uncertainties. Quick-change mold systems are a prime example of this flexibility. These systems allow operators to swap out molds for different 10L spray bottle designs in a matter of minutes, compared to the hours it took with traditional machines. Whether it's a bottle with a different spray nozzle configuration, a ergonomic grip design, or a unique label panel, the machine can adapt to the new design seamlessly, enabling manufacturers to respond swiftly to market demands.
Another aspect of this flexibility is the ability to produce variable batch sizes efficiently. Small-batch production, which was once costly and time-consuming with older machines, is now feasible with the latest models. The machine's control system can be programmed to handle runs of as few as 500 units without sacrificing quality or increasing production costs. This is particularly beneficial for niche markets or for testing new bottle designs before scaling up to mass production. Manufacturers can now cater to specialized needs, such as custom-labeled 10L spray bottles for promotional campaigns or limited-edition products, without incurring significant overheads.
Empowering the Workforce: Human-Machine Collaboration
The evolution of the 10L Spray Bottle Extrusion Blow Molding Machine is not about replacing human operators but empowering them through better collaboration. The user interface of these machines has been completely redesigned to be intuitive and user-friendly, with touchscreens that display real-time production data in a visual and easy-to-understand format. Operators no longer need to sift through complex technical manuals to make adjustments; the interface provides step-by-step guidance for tasks such as mold changes, parameter setup, and troubleshooting.
Furthermore, augmented reality (AR) technology is being integrated into some machines to assist operators in maintenance and training. By wearing AR glasses, operators can see virtual overlays of the machine's internal components, highlighting areas that need inspection or repair. For training purposes, new operators can follow virtual step-by-step instructions for setting up the machine or performing routine maintenance, reducing the learning curve and ensuring that tasks are performed correctly. This human-machine collaboration not only improves operational efficiency but also enhances job satisfaction among operators, as they are equipped with the tools and support they need to excel.
In summary, the 10L Spray Bottle Extrusion Blow Molding Machine is evolving into a symbol of modern manufacturing—one that balances efficiency with environmental stewardship, embraces smart technologies for better decision-making, and prioritizes flexibility to thrive in a dynamic market. As it continues to adapt and innovate, it will remain an indispensable asset for manufacturers looking to meet the demands of today's consumers while building a sustainable future for tomorrow.

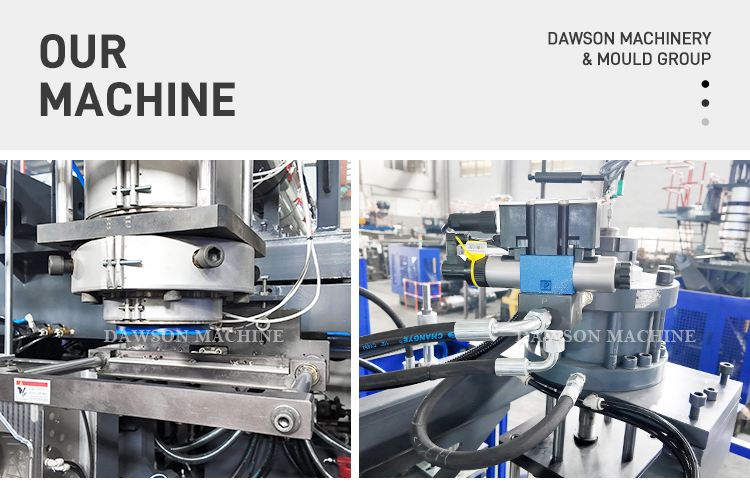
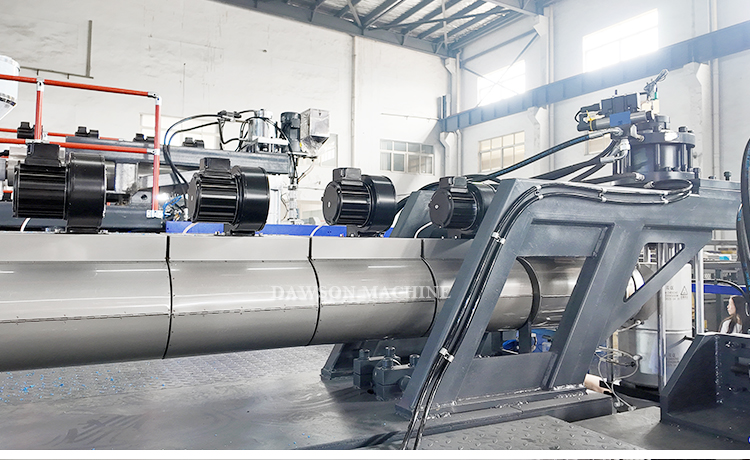
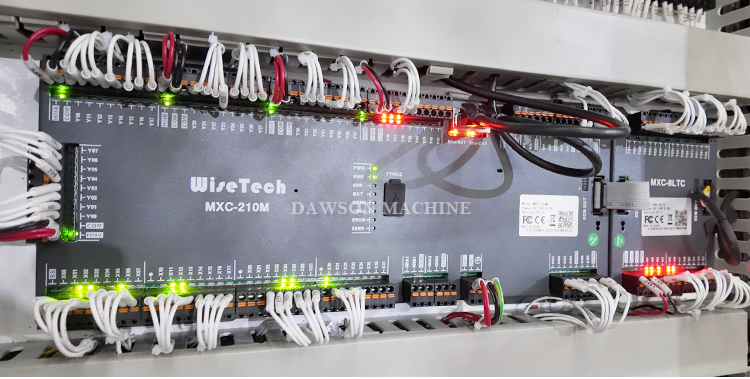
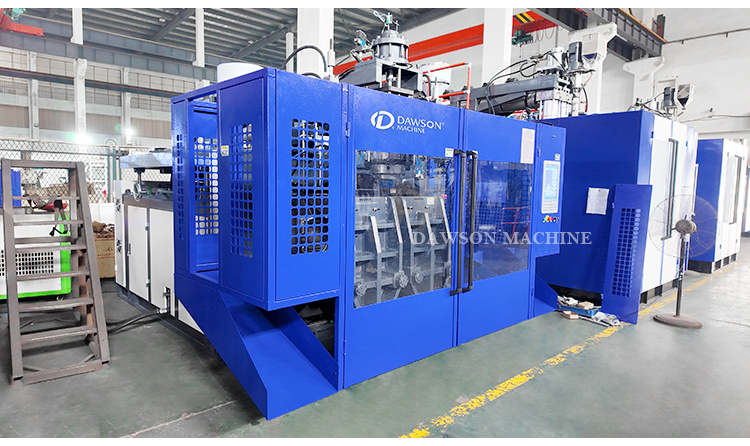
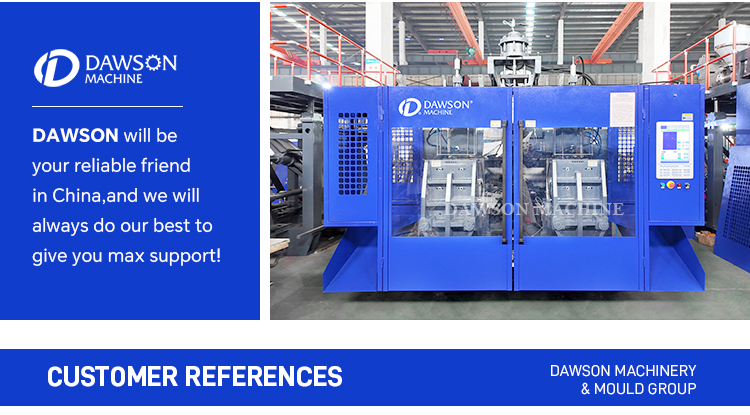
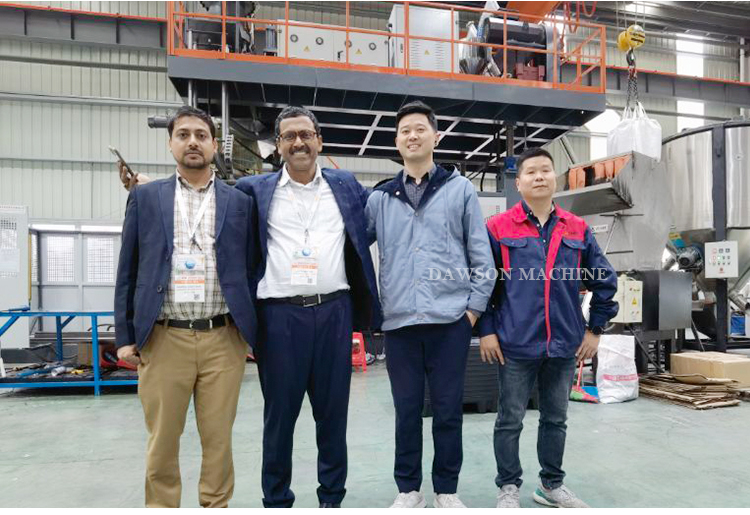
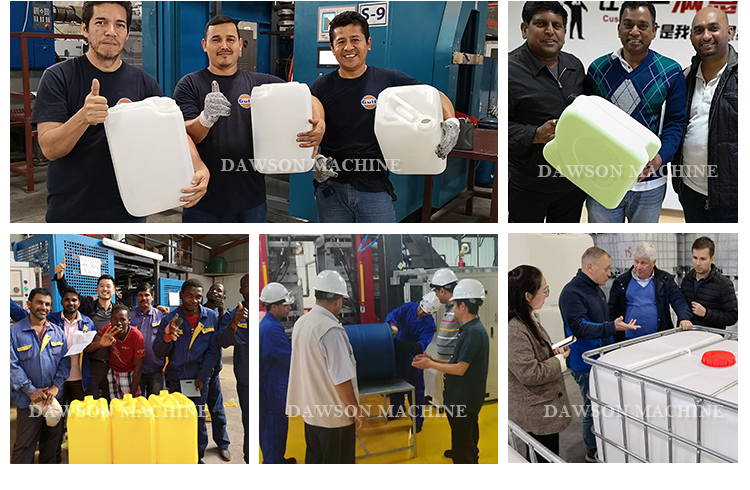
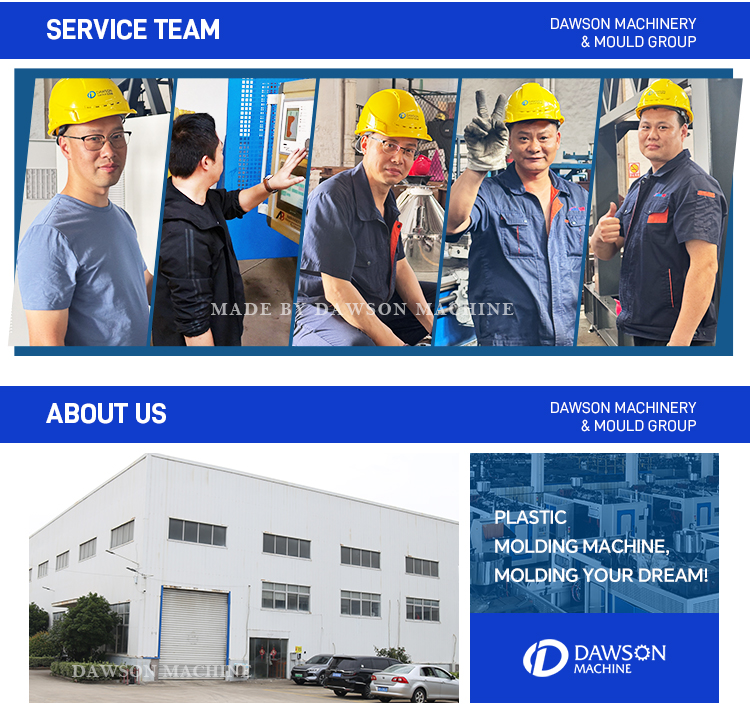
DAWSON MACHINE & MOULD GROUP
located in Zhangjiagang city, have more than 18 years' experience in the field of plastic machinery,
injection molding machine, blow molding machine, PET blow molding machine, injection blow molding machine, during the past 18 years, we always force our energy into new areas of plastic machinery, plastic packaging machinery, to update the technology, to learn advanced experience, to confirm new theory and new design, we are forming a unique competitive advantage of our owns.
The machines from our company carry good quality and effective after-sales service, upon the market,
customers from more than 45 countries, we provide complete solution for your plastic industry
business, as well as all sorts of technical support & after-sale services!
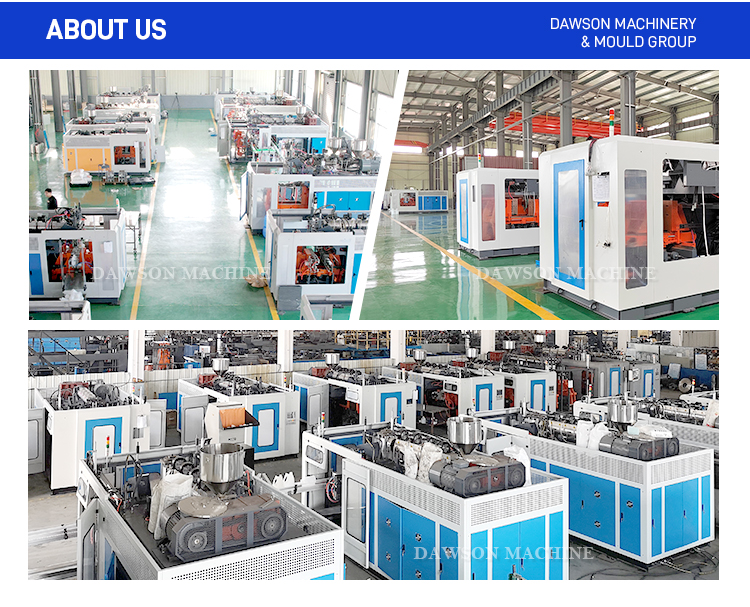
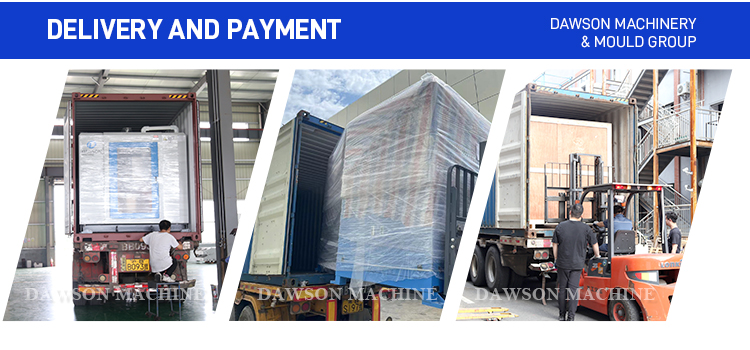
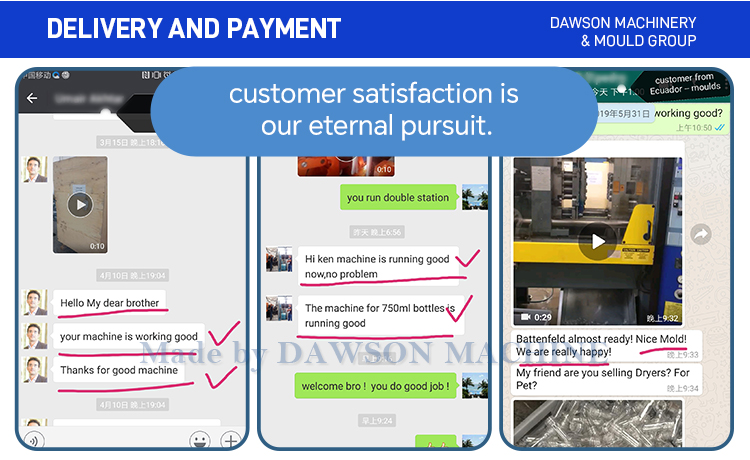
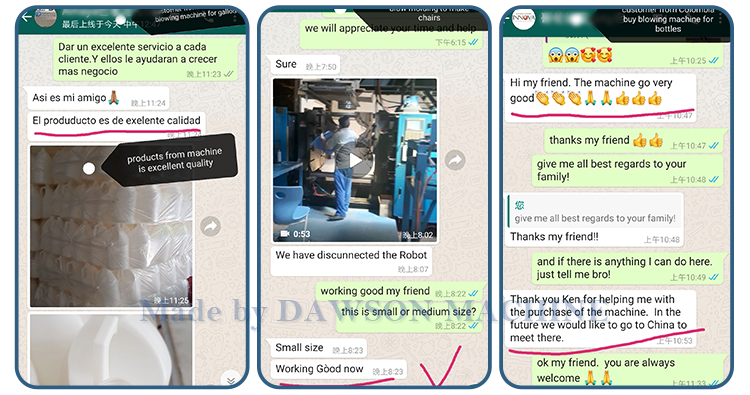
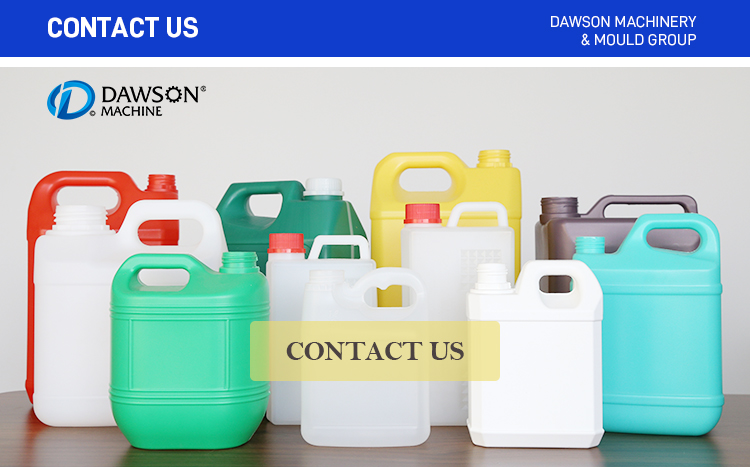